Hydra
A mobile test stand that enabled rapid, safe, & reliable of testing of liquid rocket engine(s).
Summary
The lab’s main project when I became co-lead of LPL in 2017 was a new mobile test stand (Hydra). I oversaw the design of Hydra’s original feed system and led the procurement and fabrication. Hydra is now operational, fired multiple rocket engines, and is a key enabler of training incoming members. I was a co-author of a publication about this test stand that was presented at the 2018 AIAA Propulsion & Energy Conference.
“Hydra - Development of a Liquid Rocket Engine Test Stand & Feed System”
Motivation
During my first semester as a member of LPL (August 2016), I participated in static fires with the lab’s current test infrastructure. The lab was unable to demonstrate a successful static fire thus far with our Blue Steel Engine. Upon investigating a potential root-cause , I discovered numerous safety concerns & design flaws. Instead of modifying the current test infrastructure, I decided to develop an entirely new mobile test stand when I became the laboratory co-lead in January of 2017.
Roles
Design of Feed System (Propellant Lines)
CAD Generation of Feed System
Procurement of Components, Fittings, & Instrumentation
Fabrication & Assembly of Feed System
Ensure Cleanliness for Oxygen Use
Manage Test Stand Modifications
Fluid Schematic
In the initial stages of the Hydra project, I was in charge of the entire feed system. I was responsible for developing a feed system that would deliver the required mass flow rate and injection pressure to the lab’s Blue Steel Rocket Engine, which utilized kerosene & gaseous oxygen as propellants. To begin, I illustrated a top level overview of the feed system with all of its respected components in a Plumbing & Instrumentation Diagram (P&ID). This P&ID laid out the relative order of all the valves, filters, and instrumentation required to monitor an engines performance and health. Through the months that followed, Hydra would become relatively more complex and can be seen through the revised P&IDs below.
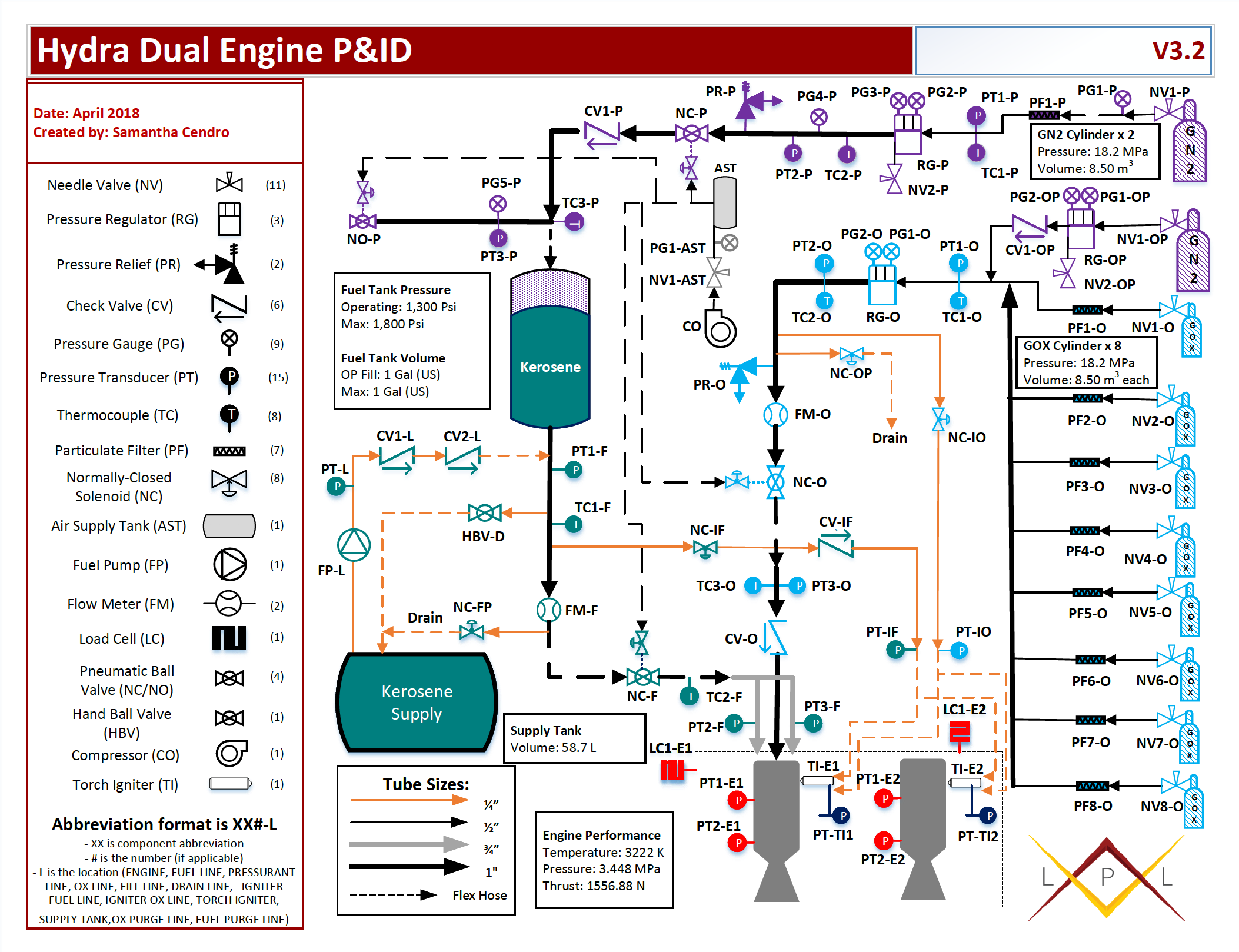
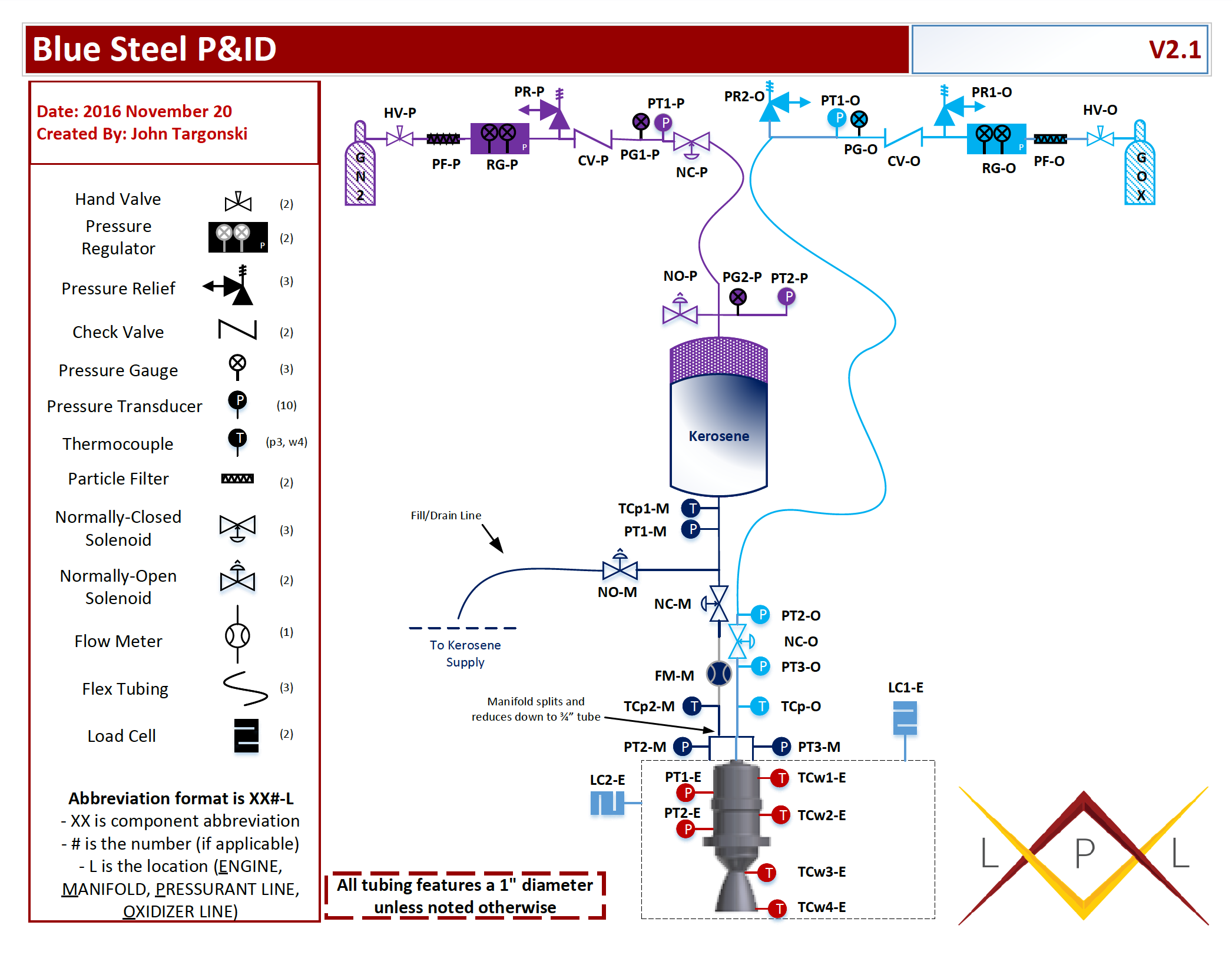
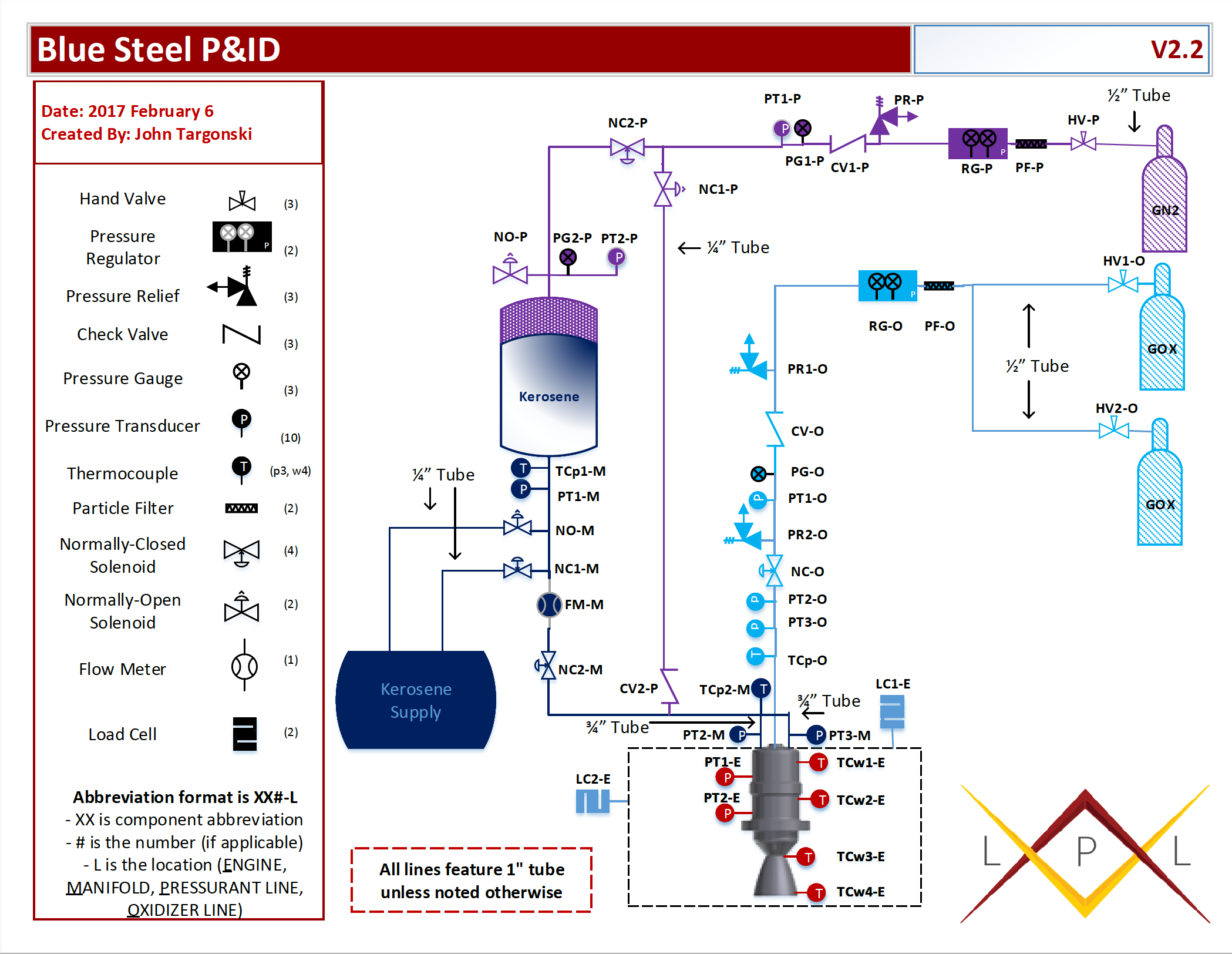
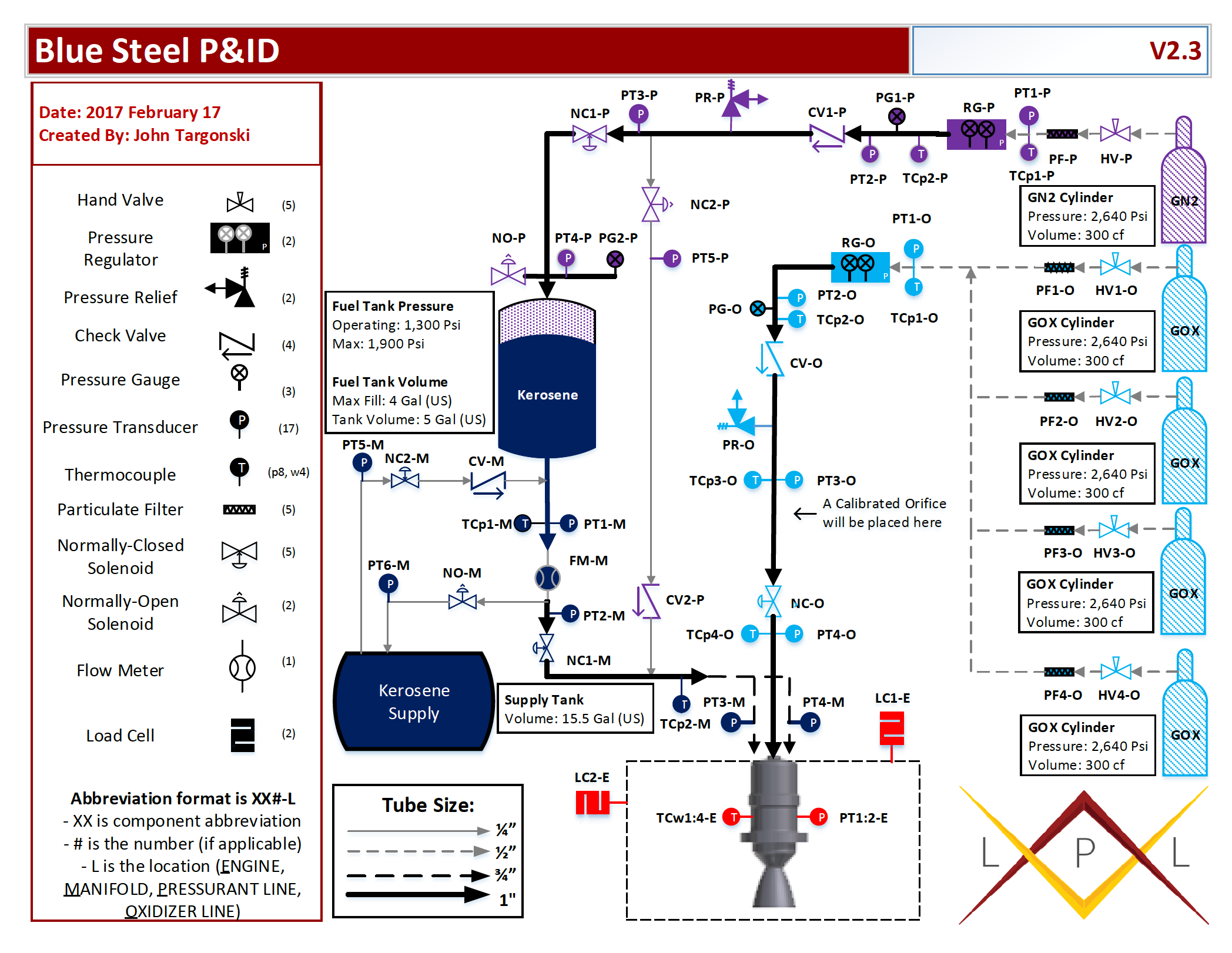
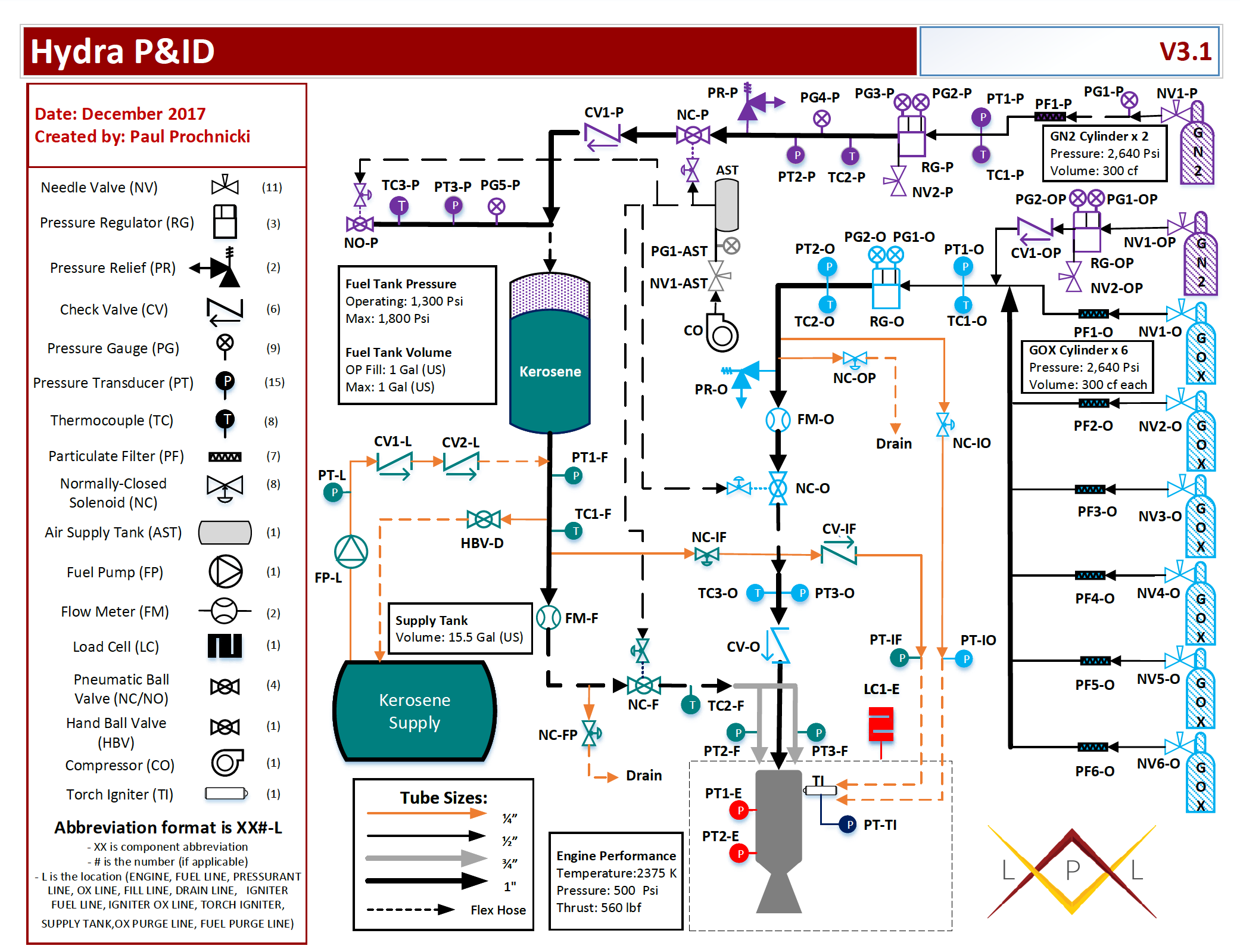
CAD Generation
I was responsible for owning & generating the 3-dimensional design of Hydra’s propellant lines. Upon sizing & procuring all components & instrumentation, I utilized Siemens NX to generate a high fidelity assembly. Mounting positions, accessibility, and ease of fabrication where all taken into account.
Determining a Set Pressure
The regulators on Hydra are manual piston sensing pressure-reducing regulators, which are prone to seat load drop, droop, and the supply pressure effect. This means that the outlet pressure will instantly drop once the flow increases from zero, change as a function of mass flow rate, as well as change in real time as the supply pressure decreases. The regulators are open loop and do not provide feedback to correct for this. As a result, you need to account for this during procurement and operation. This is determined by analyzing a regulator’s flow curve. I presented how to analyze and determine how to set the regulators by using the nominal operating conditions for the Jessie or James engines as an example.
Procurement, Fabrication, & Assembly
With prior experience in fabricating test stands, I taught members how to successfully build a test by leading the Hydra build. I procured all fittings, components, instrumentation for the original version of Hydra. Once everything arrived, I taught current members how to cut, bend, and swage tubing as well as how to assemble compression and NPT fittings. I also taught members about the potential hazards when using an oxygen system and how to select components and ensure cleanliness for safe operation. This and more was included in a presentation I gave to our lab called the “Introduction into Propellant Feed Systems” in February of 2017.
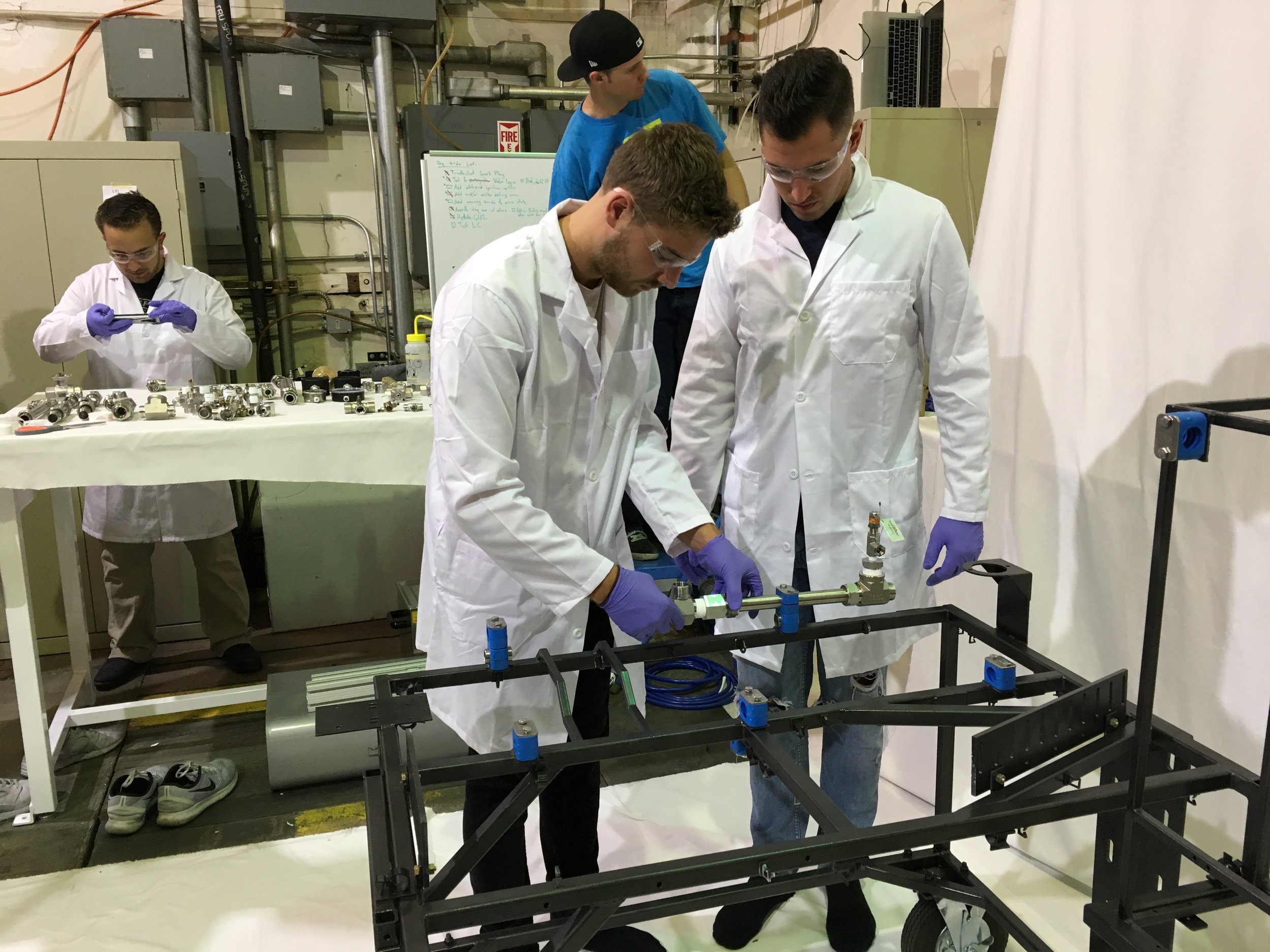
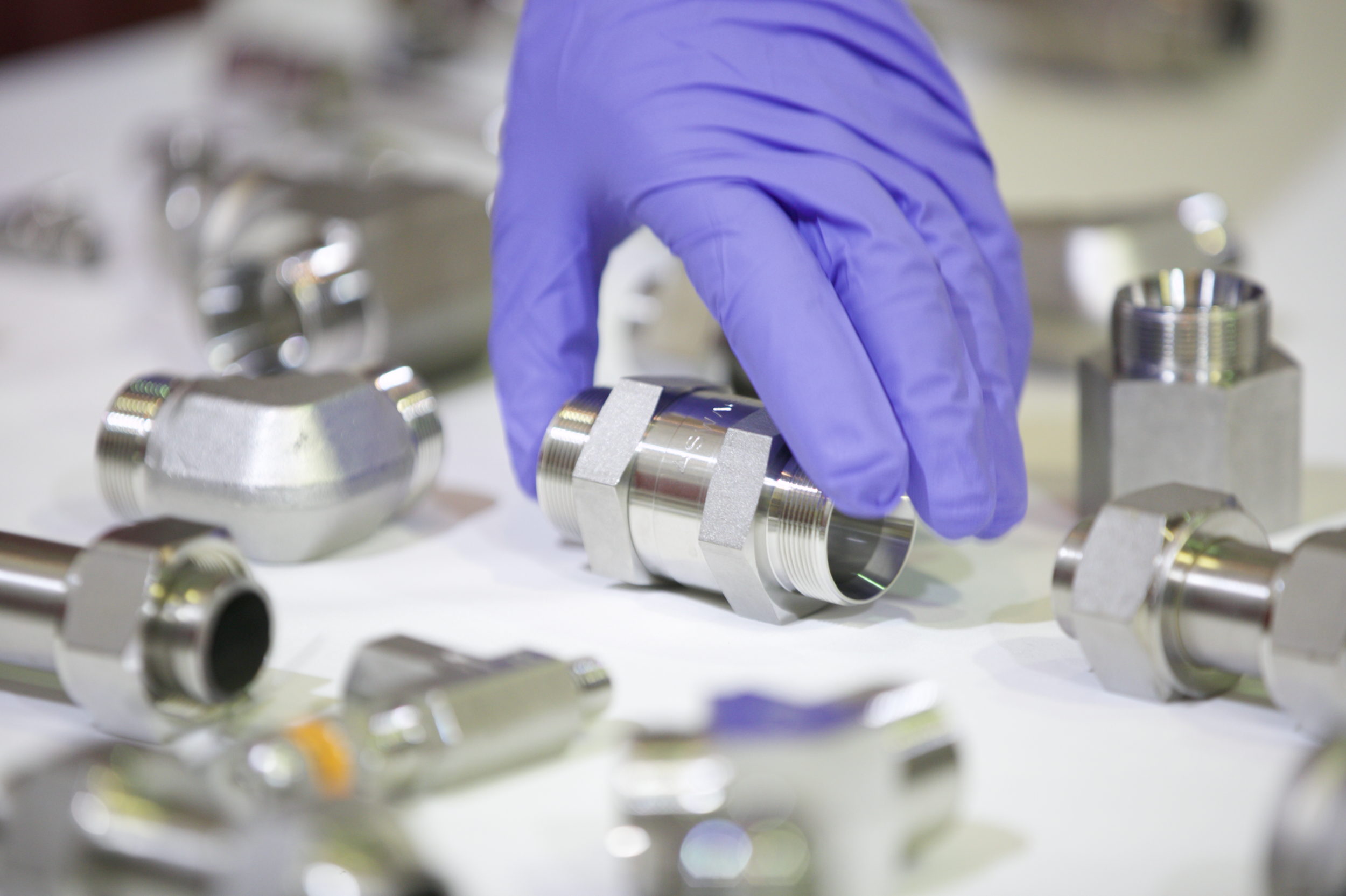
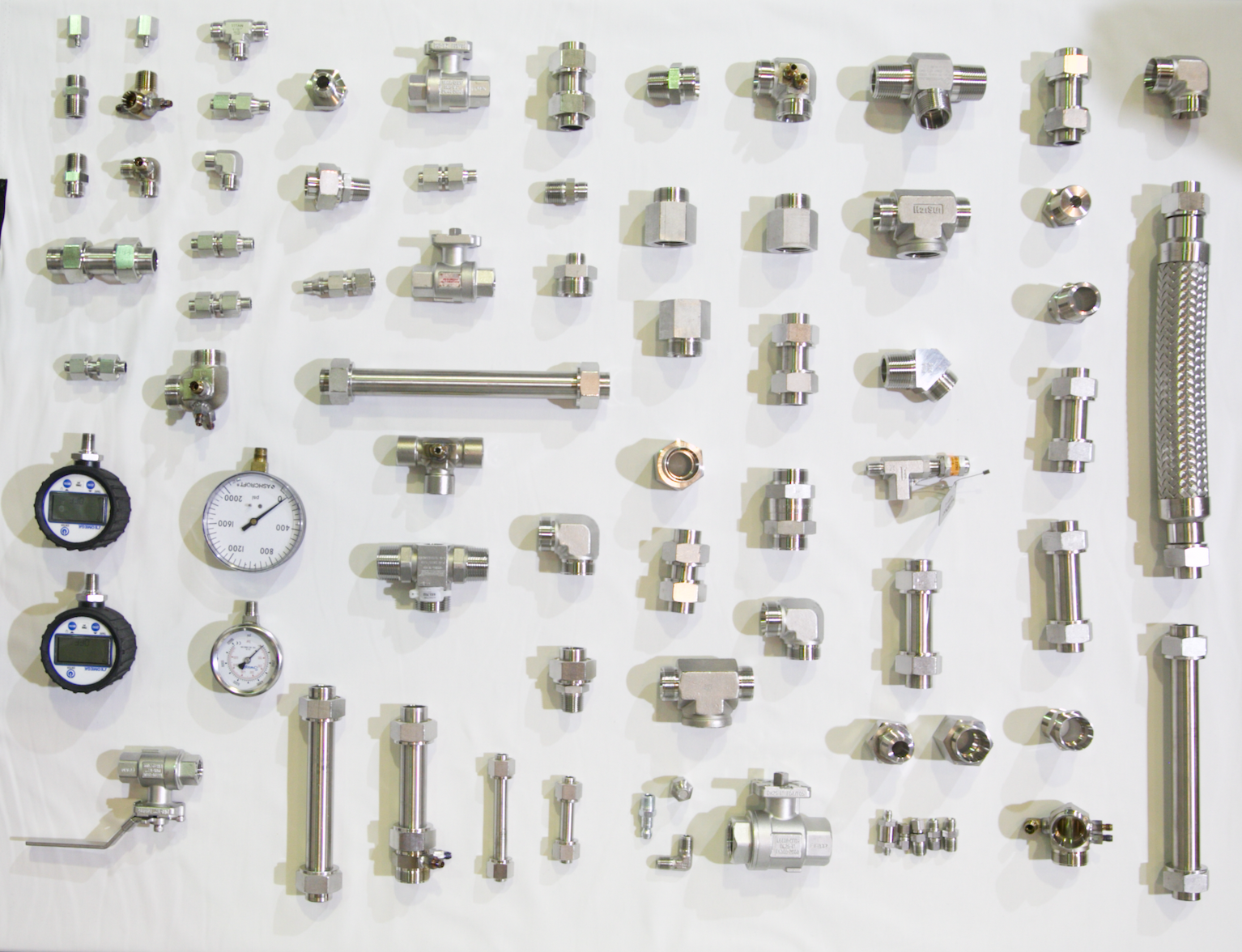
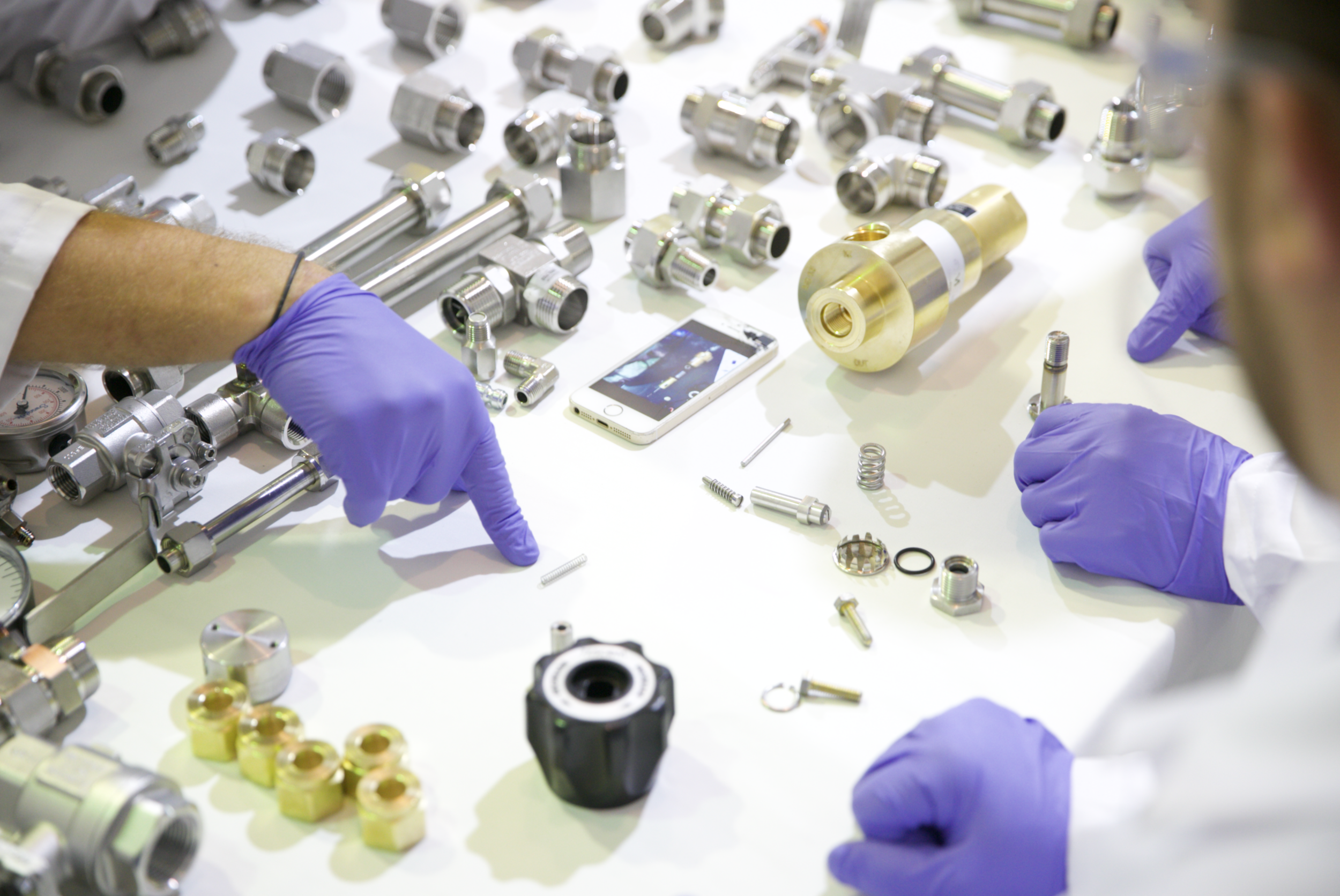
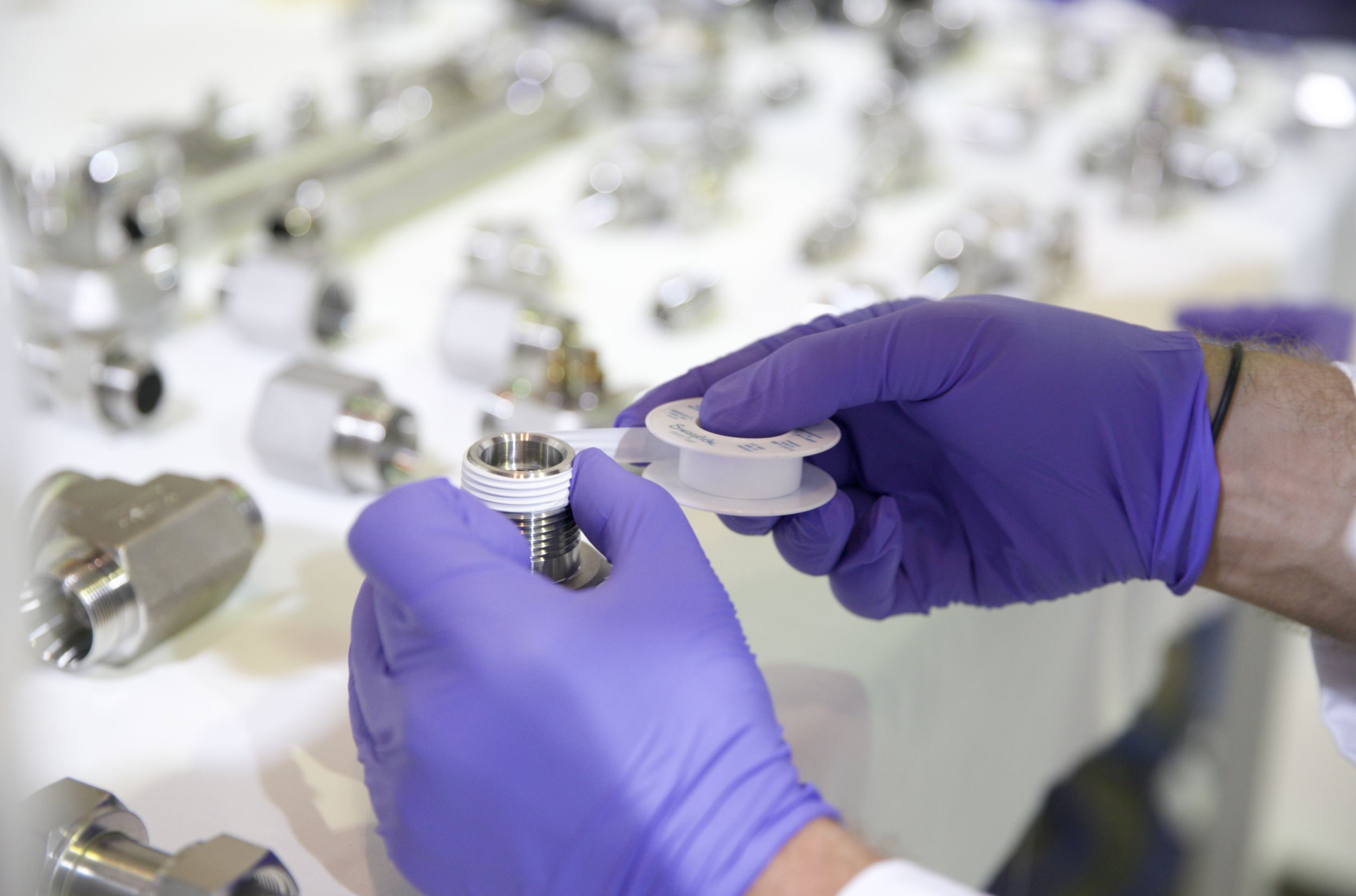
Activation of Hydra
On December 2, 2017, the laboratory brought Hydra to the Friend’s of Ametury Rocketry test site in Mojave, California for its inaugural static fire. With the lab’s currently retired Blue Steel 2.0 rocket engine, Hydra performed nominally and LPL experience their first successful static fire. Today Hydra is still operational and is currently utilized to test the laboratory’s Jessie & James rocket engines.
Hydra Modifications
Today Hydra still serves a vital role to continue and push LPL’s main mission of workforce development. Hydra is a training tool that new members can learn from through operation & modifications. During my final semester of graduate school, January-May 2018, I was the in charge of overseeing all modifications on Hydra. I brainstormed modifications that would be useful & required to eventually static fire two engines simultaneously. From there, I delegated individual projects to new and returning members. I met with each person 1:1 every week to maintain a schedule, aid in roadblocks, and help answer any questions. Some modifications included a new manifold to house 8 oxygen cylinders, a new dual engine mount, new propellant lines for dual capacity, & upgrades to functionality of the data acquisition & controls software.